EMDD Universal – Arrives On Time at Birmingham New Street Station
Built in 1966, Birmingham New Street Station is currently undergoing a huge refurbishment and EMDD-UNIVERSAL, has played a major part in the transformation of the new ‘Gateway to Birmingham.’
Phase one of the works carried out involved the complete removal of one level of the multi-storey car park situated above the twelve platforms of the station, to create a full height departure and arrivals lounge. EMDD-UNIVERSAL concrete cutting specialists of thirty years standing, were called in by demolition contractors, Coleman and Company, to give advice on the most cost effective and efficient way to cut and remove the entire second floor slab, including the lattice work of structural beams. Work had to be carried out without disruption to the live rail platforms beneath. There had to be no vibration, dust or noise. Diamond cutting was therefore the only option available. EMDD-UNIVERSAL calculated weights and sizes to create an accurate cutting schedule. This was complicated by the fact reinforcement details were limited, as few drawings from 1966 were available.
Nottingham based Harold Potter Ltd, lifting and handling specialist and long-term associate of EMDD-UNIVERSAL, were called in to devise a method for lifting the cut pieces of concrete. Taking into account strict floor loadings and limited headroom, they designed, manufactured and installed a four crane system, to handle ten tonne blocks. The cranes, capable of moving in any direction, would gently lower each block onto a bogie system, to be taken from the building for disposal by the demolition contractor following cutting operations.
The contract period was eight months and during that time EMDD-UNIVERSAL efficiently completed diamond sawing,
drilling and crunching on what is believed to be the largest concrete removal project in Europe.
EMDD-UNIVERSAL removed 7,500 tonnes of reinforced concrete
In order to effectively plan the concrete cutting and robotic demolition works at Birmingham New Street Station, EMDD-UNIVERSAL spent over 100 hours producing an in depth cutting schedule which identified every concrete section to be removed. A cutting program of almost 1000 pieces of concrete was devised. Due to weight and transport restrictions, no single piece of concrete could be longer than 6m, wider than 3m or heavier than 10 tonnes. The Mezzanine slab structure that was to be removed was predominantly made up of 4 different elements, those being primary beams, secondary beams, 150mm concrete slab and 400mm concrete slab. Beams ranged in size with primary beams between 1.2m and 2.2m wide and secondary beams being 0.6m wide. Both Primary and Secondary beams were 870mm thick. To remove cut sections of concrete from site, a track mounted crane system was designed, manufactured and installed. A bespoke structural supporting system was also developed to support concrete sections during the cutting and removal process.
EMDD-UNIVERSAL floor sawed 4,000 linear meters, 150mm and 400mm deep
To carry out the concrete cutting and removal of sections of 150mm and 400mm thick reinforced concrete slab, both diesel and 3 phase floor saws were utilised. Sections of concrete were secured to the overhead crane via the pre-drilled lifting holes and separation cuts were made to release the concrete.
Concrete sections were then lowered and transported out of the building on the bespoke bogies or lifted
and transported by the demolition contractor to removal vehicles using the crane system.
EMDD-UNIVERSAL drilled 3000 holes, 100mm diameter to 200mm diameter
Various diameter holes were drilled through both 150mm and 400mm concrete slab sections to prevent overcutting into primary and secondary beams and to aid lifting. In order to remove risk to other workers from falling concrete cores, every hole was pilot drilled so the precise hole locations could be determined from the underside of the Mezzanine slab. Genie hoists and catchment trays were then erected to collect all cores and slurry.
EMDD-UNIVERSAL wire sawed 1000m² of reinforced concrete
With reinforced concrete beams up to 2.2m wide and 870mm deep there was a need for over 600 separation cuts through the heavily reinforced beams. The quickest and most efficient method of forming these separation cuts was the use of diamond wire saws. The wire saw cuts were made from the top, side or underside of the beams depending on the size of the beams and structural support system being used. EMDD-UNIVERSAL utilised Tyrolit SB, WCE 14 and SK B wire saws during the cutting, depending on the size and the location of the cut. EMDD-UNIVERSAL also devised and utilised a bespoke water collection system, which prevented water spray and collected 80% of all slurry created, the balance being retrieved with wet vacs and deposited into collection tubs ready for recycling. EMDD achieved an average wire saw cutting time of 40 minutes per 1m2 of reinforced concrete.
EMDD-UNIVERSAL wall sawed 750 linear meters of reinforced concrete
Due to extensive structural strengthening of existing vertical columns there was a need to remove 320 non-structural concrete column nibs without damaging the integrity of the remaining concrete structure. Existing drainage had to be diverted before a Tyrolit WX 15 wall saw could be used to form a separation cut through the 200mm thick concrete. Separated sections of concrete were then crunched and removed carefully using a Brokk 90 machine.
EMDD-UNIVERSAL purified 1,000,000 litres (1,000 tonnes) of concrete slurry
Producing an average volume of 4000 litres of concrete slurry daily, a practical and cost effective recycling solution had to be found. Wastewater management specialist, Siltbuster was identified as the preferred solution provider. Due to space and weight restrictions at Birmingham New Street Station, it was decided the Siltbuster HB10 unit was the most suitable for the project. The HB10 recycling unit stills the incoming water and routes it over a set of inclined plates. Fine particles settle onto the plates and slide down to the base for collection, while treated water flows to an outlet weir. The treated water produced was either disposed of down drains or wherever possible reused as part of the concrete cutting processes. The waste product collected by the HB10 was a thick, toothpaste like concrete paste that was disposed of with all other concrete spoil. The HB10 unit was set up with a bespoke slurry holding tank system devised by EMDD-UNIVERSAL so that 3000 litres of slurry could be held at any one time. This system reduced the need for constant management of the slurry recycling system.
EMDD-UNIVERSAL robotically crunched 350 tonnes of reinforced concrete.
Where diamond cutting techniques could not be utilised, robotic demolition machines were used to crush areas of concrete slab and beams. Various Brokk machines were used including Brokk 90, Brokk 180 and Brokk 260 models. The Brokk 260 was used to remove 1500 M2 of concrete slab and beams from above the main service spine which houses all communication cables for Birmingham New Street Station.
Clearly this was a very delicate and sensitive operation. The 260 has a crushing capability of 500mm.
The final remarkable thing – EMDD-UNIVERSAL finished this incredibly complex project ahead of schedule!
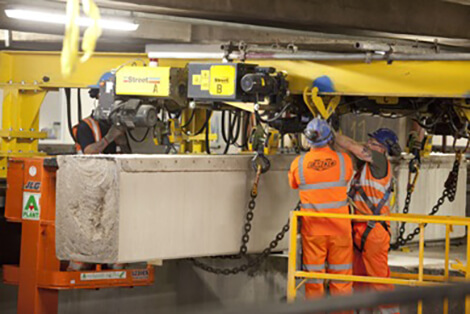
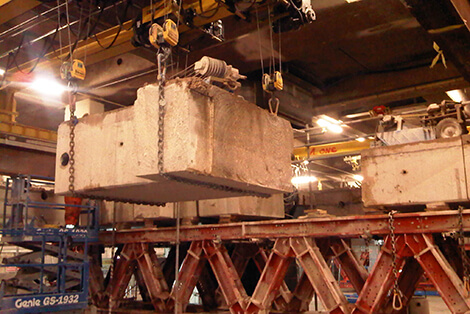